Experimental Plasticity and Metal Forming
![]() |
Toshihiko KUWABARA Department of Mechanical Systems Engineering Keywords: anisotropy, constitutive modeling, formability, material testing, simulation Phone & fax: +81-42-388-7083/ +81-42-388-7425 E-mail: kuwabara*cc.tuat.ac.jp (chage "*" to "@" to send E-mail) URL:http://www.tuat.ac.jp/~kuwabara/ |
Motivations
Product development cycles have been shortened recently, making the use of traditional empirical approaches for determining optimum forming conditions inappropriate. The goal in manufacturing must be to establish “prototype-free” manufacturing. Accordingly, there is a need for accurate simulation techniques for metal forming using finite element analysis. For accurate and time-effective finite element simulations, it is vital to use accurate phenomenological plasticity models based on anisotropic yield functions. The responses of materials to a variety of loading modes have been of interest for at least a century. Many anisotropic yield criteria and constitutive models have been proposed to date. However, experimental evidence is often lacking, particularly for materials in industrial use.
In sheet or tube forming processes, materials are generally subjected to multiaxial loads. Moreover, metal parts are very often manufactured in two or more forming stages. Therefore, multiaxial and/or multistage loading tests are infinitely preferable for checking the plasticity models to be used in simulations. Servo-controlled testing machines are necessary for such tests. Although not categorized as multiaxial tests, in-plane compression tests or in-plane stress reversal tests are effective in observing and modeling the strength differential effect and the Bauschinger effect of sheet metals. These tests are also important from the industrial point of view, because such modes of deformation are very common in sheet forming processes, including deep drawing and draw-bending.
The research activities of my laboratory mainly focus on following items:
- To develop novel material testing apparatus, as shown in Fig. 1, for precisely measuring the anisotropic plastic behavior of metal sheets and tubes under a variety of loading paths. Particular attention is focused on the plastic response to multiaxial loading, multistage loading and in-plane reverse loading.
- To validate phenomenological constitutive models (anisotropic yield criteria and its associated/non-associated flow law) through the comparison of observed material responses with that predicted using phenomenological plasticity models.
- To establish methodologies for accurate FEM simulations based on refined material models.
- To evaluate the forming limit strains and stresses of sheet metals and tubes using both experimental and analytical approaches.

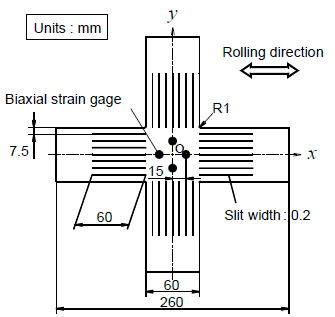
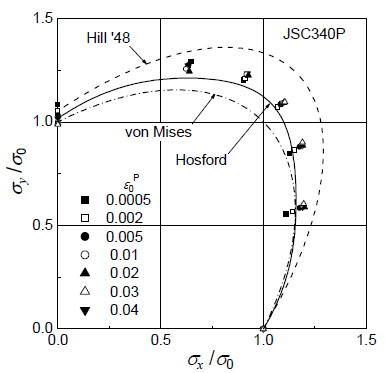
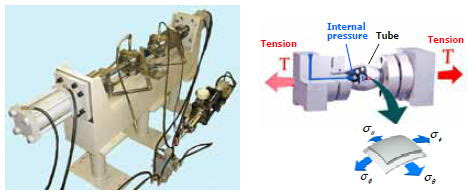
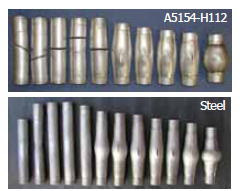
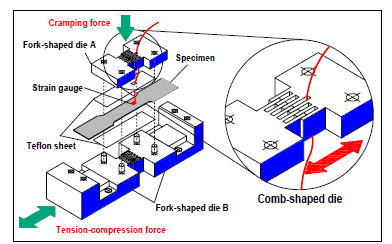
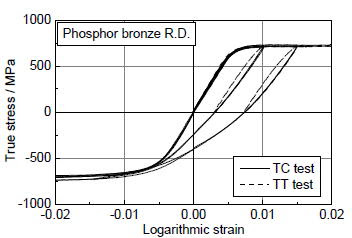
Fig.1 Material testing apparatus developed in my laboratory:
(a1) Servo-controlled biaxial tensile testing apparatus for sheet metals;
(a2) cruciform specimen;
(a3) measured yield points (high strength steel);
(b1) Servo-controlled biaxial stress testing apparatus for tubular materials;
(b2) Fractured specimens under linear stress paths;
(c1) In-plane reverse loading testing apparatus for sheet metals;
(c2) Measured Baushcinger curves of a copper alloy